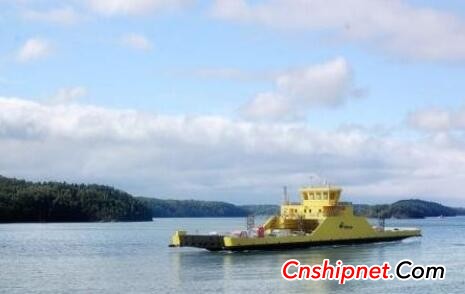
Diamond Lapidary Glass Grinding Wheel
Of the several methods now used for fixing super abrasive particles of diamond or CBN to the working surface of an abrasive tool, electroplating is the fastest growing.More and more production operations involve combinations of hard-to-grind materials and complex wheel shapes that virtually dictate the use of electroplated super-abrasive tools.
Characteristically,such tools consist of a precision tool form or mandrel with super-abrasive particles deposited on the working surface and locked in place by electrode position of a bonding matrix,most frequently nickel.The particles are so locked onto the tool surface may vary in size and dispersion to suit the purpose of the tool, but they should lie in a single layer.
Electroplated grinding wheels with nickel bonding can achieve high stock removal rates and high-precision profiles on parts being ground. Depending on the wheel blank design,plating technique, and post-treatment of the single-layer grit structure, many different grinding wheels can be produced using this bond system.There is no need for dressing during the life of the wheel.This avoids downtime and eliminates the need for a dressing device.
When you need to remove more material than polishing will allow,use quality grinding wheels.Diamond grinding wheels are used for grinding, shaping,flattening or smoothing of your specific application of stone.The Diamond Tool Store offers a full line of diamond grinding and shaping wheels for many applications that come in many different sizes with desired grits and positions.The product line you will see for grinding tools will reduce the amount of chipping and special shapes and sizes that allow fabricators to get into tight corners for a clean,smooth finish.
Our electroplated grinding wheel are precision engineered to meet the high demands of lapidary,jewelry,gemstone,glass,ceramic,composite,electrical contacts of starters,alternators, motors applications.We offer many stock wheels with varying shapes and grits that will maintain tight tolerances and provide superior form holding when used wet or dry.
Metal Bond Grinding Wheels and Diamond Sintered Grinding Wheel are manufactured using a variety of metal fillers with Diamond or CBN abrasive. Generally, Metal Bond wheels have the hardest matrix, and require coolant.
Diamond CBN Superabrasive Grinding Wheels are available in a variety of sizes and styles, both plain and formed to specific contours. These grinding wheels are designed primarily for grinding such materials as: high carbon; high chrome; high speed steels, such as M2, M3, M7 and T15; die steels, such as: D2, D3, HB, A & O; alloy steels (harder than 50 Rc); nickel and cobalt base super alloys; titanium; stainless steels, etc.offer substantial benefits in grinding exotic alloy steels. Since the CBN crystal resists dulling much better than conventional abrasives, it provides stress-free, cool cutting action throughout its long life. The crystal tends to be self-sharpening as cutting stress increases. The mono-layer wheel structure requires no truing or dressing throughout its life, thereby eliminating truing tool cost as well as non-productive wheel truing time.In addition to this,we also provide the lapidary polishing wheels.
Diamond Grinding Wheels, Lapidary Grinding Wheels, Diamond Grinding Wheel, Diamond Flat Wheel, Diamond Spherical Grinding Wheel, Diamond Textured Wheel, Diamond Profile Wheel, Diamond Engraving Wheel
Hans Superabrasive Material Co., Ltd. , https://www.hansuperabrasive.com