Abstract: The HID618A series injection molding machine servo driver specially developed by Hekang, with its superior performance and excellent quality, has effectively solved the shortcomings of traditional injection molding machines, such as low precision, high noise, high oil temperature and waste of electrical energy. The industry has played an invaluable role in saving energy and reducing consumption and improving product accuracy, bringing tremendous economic benefits to the company. This article mainly introduces the batch application of Hekang HID618A series injection molding servo driver in Gudi technology injection molding machine.
Keywords: Hekang Servo Drive Injection Molding Machine Energy Saving Introduction: Traditional injection molding machines, known as “electric tigers,†use less than 50% of energy, and electricity costs often account for a considerable proportion of the cost. Hekang HID618A series special servo driver for injection molding machine adopts new servo control technology. Through flow and pressure double closed-loop control and precise PID algorithm, it replaces the valve control of traditional injection molding machine asynchronous motor quantitative pump, and is given according to the real-time signal of flow and pressure. Accurately control the output of the motor and effectively control the energy waste caused by the high-pressure overflow of the injection molding machine. This not only saves electric energy, but also reduces oil temperature.
I. High-volume application of HID618A series servo driver on Gudi Technology Injection Molding Machine 1. Brief Description of the Application Location: Ezhou Gudi Technology Co., Ltd., Chongqing Gudi Plastic Electrical Appliance Co., Ltd. Driver Model: Hekang HID618A Series Injection Molding Machine Dedicated Servo Drive System Name: Injection Molding Machine, Tonnage from 90T to 600T
Motor Model: Synchronous Motor, Power Stage 11kW~55kW
Pump Model: Gear Pump, Displacement 32CC~125CC
Number of machines: 55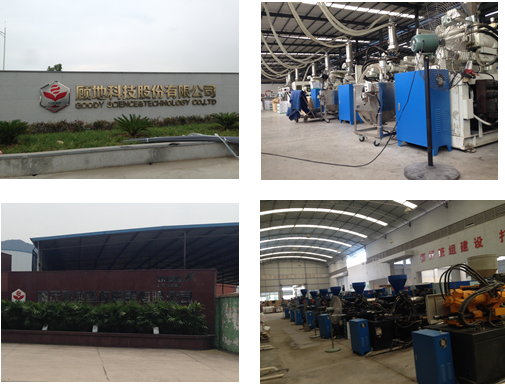
2. Control method of the original injection molding machine The control method of the original injection molding machine is the asynchronous motor supporting the quantitative pump and the proportional pressure/proportional flow composite valve (PQ valve). When the system is working, the analog pressure and flow control signals output by the injection molding electronic control system are used to achieve continuous and proportional control of system pressure and flow. In the working process of an injection molding machine, the speed and pressure of various actions need to be continuously changed during each cycle to adapt to the pressure, speed, and time control requirements of the injection molding process. The PQ valve system meets the control requirements of the injection molding machine's opening and closing die speed, injection speed, screw speed, injection pressure, pressure holding pressure, screw torque, ejector force, etc., but there are more throttling losses and overflows during system operation. Loss of flow, and therefore greater power loss, especially for some products with higher holding pressures and longer holding times, the performance is more pronounced.
In actual operation, many Gu Di technology machines produce PPR pipe joints, and the holding time is usually 15 to 20 seconds. At this time, the flow rate required by the system is very small, and the asynchronous motor and the quantitative pump are output at the maximum flow rate as long as they work. Excess flow is discharged through the PQ valve back to the tank, doing no work, and also increases the oil circuit overflow cycle, so that the oil temperature rises. There is cooling in similar processes. No flow and pressure are required for cooling. The oil path of the original system is completely returned to the tank through the PQ valve, doing no useful work, wasting energy.
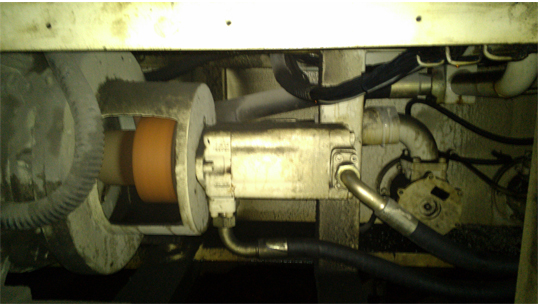
3, HID618A series servo drive energy saving control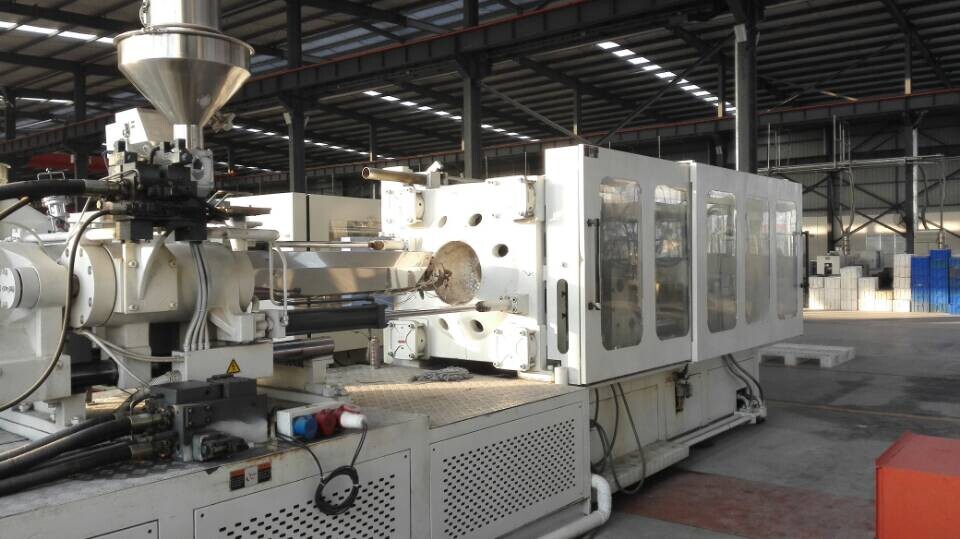
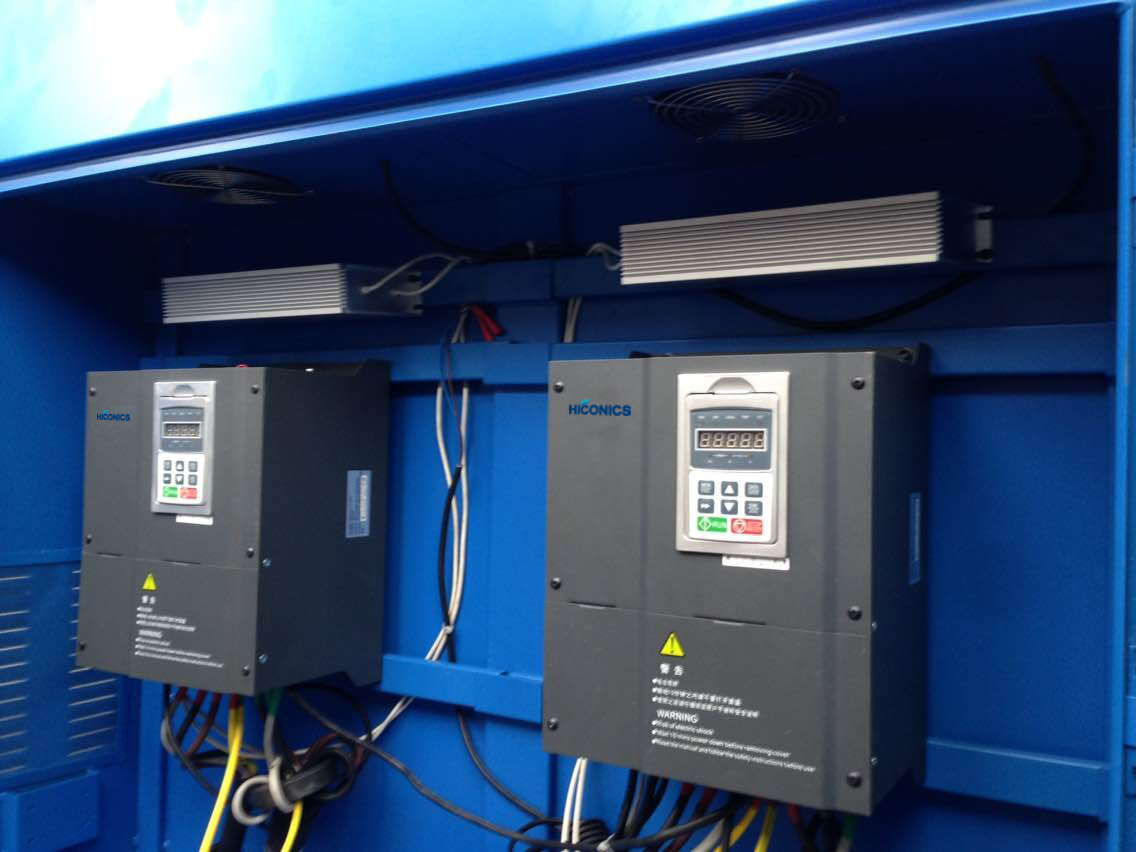
According to the current situation of large oil spillage at the operation site and serious waste of electrical energy, Hekang technical personnel recommended installing HID618A series servo drives for energy-saving transformation, replacing the original asynchronous motor with a synchronous motor with higher control accuracy and higher response accuracy, and quantifying the original The pump is replaced by a servo gear pump. Pressure sensors and rotary transformers are added to the system. The system intelligently extracts the pressure and flow analog signals from the injection molding machine. Through precise algorithms, the pressure and flow angle feedback feedback pressure and flow simulation are compared. Doing PID adjustment to achieve flow, pressure double closed-loop control, on-demand control output, not only greatly reduces the power loss, but also reduce the overflow of the oil circuit, reduce oil circuit, reduce oil temperature, and effectively extend the life of the injection molding machine. The single machine energy-saving rate is up to 60%, and the average energy-saving rate is above 35%.
4ã€HID618A series servo driver installation method A, main circuit connection:
The power cable is connected to the main circuit RST of the driver, the motor cable is connected to the main circuit UVW, and the brake resistor line is connected to the driver's main circuit "+" and "PB". The ground wire is connected to the main circuit PE of the driver. The motor fan wire is connected to the main circuit terminal RST or other three-phase power supply.
B, control board signal line connection:
Positive pressure signal line is connected to the control board AI1, the negative electrode is connected to the control board GND;
The positive of the flow signal line is connected to the control board AI2, and the negative pole is connected to the control board GND;
The positive pressure sensor is connected to the control board 15V, the negative electrode is connected to the control board AI3-, and the signal line is connected to the control board AI3+;
The motor temperature output line is connected to the control board DI6 and COM;
Injection molding machine motor enable signal line received control board DI1 and COM;
The encoder cable is connected to the control board DB9 port.
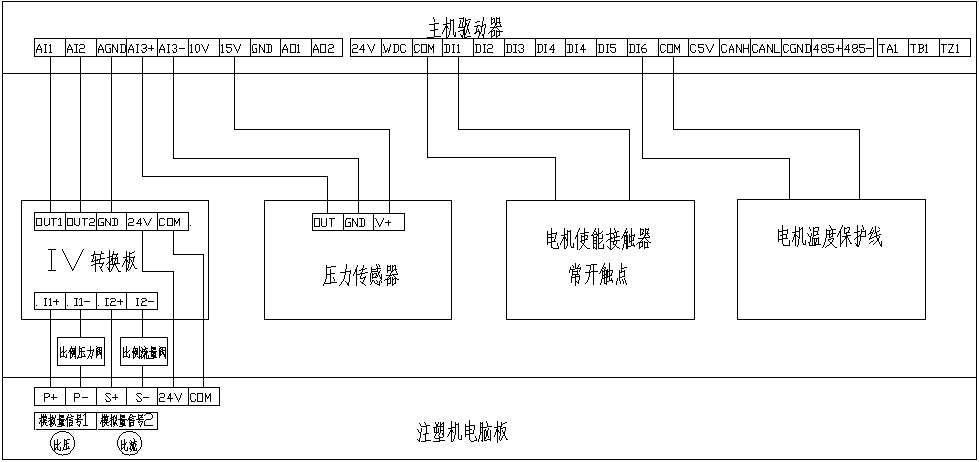
Second, the HID618A series of drivers in the Gu technology application of the effect of a high energy-saving rate. Gudi's injection molding products are mainly PPR and UPVC pipe fittings. The HID618A dedicated drive controls the output of the motor in real time according to demand. The motor speed is almost zero when the pressure is maintained and the cooling is achieved. This saves a lot of energy for the customer. .
2, reduce the oil temperature. The HID618A dedicated drive cooperates with the servo energy-saving system to replace the system relief valve and proportional valve. According to different process requirements, different flow rates are provided on demand, which effectively suppresses the overflow of the oil circuit, reduces oil circuit circulation, and reduces oil temperature.
3, reduce noise. After applying the HID618A dedicated driver, the overall operating noise is significantly lower than that of the original asynchronous motor vane pump control system, improving the ambient noise.
4, to improve the control accuracy. HID618A dedicated driver, the application of advanced software algorithms, high control accuracy, pressure fluctuations in ± 0.5bar, product repeatability is good.
5, easy to use. HID618A servo dedicated driver, user-friendly design, easy to install and use, using common motor parameters packaged form, to avoid cumbersome motor parameter input. The pressure and flow curve calibration adopts 11 percentage sampling points. The optimization of curve calibration also brings user-friendly use.
Third, the small combination of Kang HID618A series of special injection molding machine servo drive with its outstanding performance in Chongqing Gu Di Technology and Ezhou Gudi technology batch applications of 55 units, the average power saving rate reached more than 35%, high product repeatability, stable production . After several months of operation, it has been operating stably with a 100% operating rate and zero failures. It has been highly recognized by customers and worthy of widespread promotion.
stainless steel pig trough for piglets feeding equipments
Keywords: Hekang Servo Drive Injection Molding Machine Energy Saving Introduction: Traditional injection molding machines, known as “electric tigers,†use less than 50% of energy, and electricity costs often account for a considerable proportion of the cost. Hekang HID618A series special servo driver for injection molding machine adopts new servo control technology. Through flow and pressure double closed-loop control and precise PID algorithm, it replaces the valve control of traditional injection molding machine asynchronous motor quantitative pump, and is given according to the real-time signal of flow and pressure. Accurately control the output of the motor and effectively control the energy waste caused by the high-pressure overflow of the injection molding machine. This not only saves electric energy, but also reduces oil temperature.
I. High-volume application of HID618A series servo driver on Gudi Technology Injection Molding Machine 1. Brief Description of the Application Location: Ezhou Gudi Technology Co., Ltd., Chongqing Gudi Plastic Electrical Appliance Co., Ltd. Driver Model: Hekang HID618A Series Injection Molding Machine Dedicated Servo Drive System Name: Injection Molding Machine, Tonnage from 90T to 600T
Motor Model: Synchronous Motor, Power Stage 11kW~55kW
Pump Model: Gear Pump, Displacement 32CC~125CC
Number of machines: 55
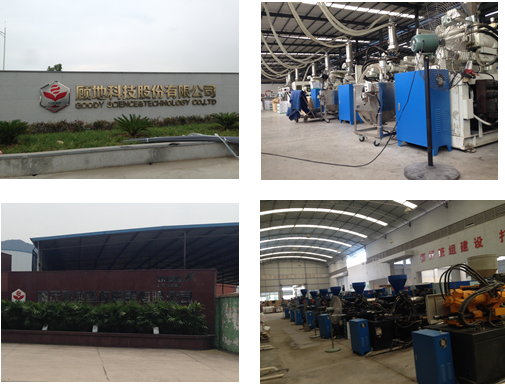
Figure 1: Application of Hikvision HID618A Servo Drives
2. Control method of the original injection molding machine The control method of the original injection molding machine is the asynchronous motor supporting the quantitative pump and the proportional pressure/proportional flow composite valve (PQ valve). When the system is working, the analog pressure and flow control signals output by the injection molding electronic control system are used to achieve continuous and proportional control of system pressure and flow. In the working process of an injection molding machine, the speed and pressure of various actions need to be continuously changed during each cycle to adapt to the pressure, speed, and time control requirements of the injection molding process. The PQ valve system meets the control requirements of the injection molding machine's opening and closing die speed, injection speed, screw speed, injection pressure, pressure holding pressure, screw torque, ejector force, etc., but there are more throttling losses and overflows during system operation. Loss of flow, and therefore greater power loss, especially for some products with higher holding pressures and longer holding times, the performance is more pronounced.
In actual operation, many Gu Di technology machines produce PPR pipe joints, and the holding time is usually 15 to 20 seconds. At this time, the flow rate required by the system is very small, and the asynchronous motor and the quantitative pump are output at the maximum flow rate as long as they work. Excess flow is discharged through the PQ valve back to the tank, doing no work, and also increases the oil circuit overflow cycle, so that the oil temperature rises. There is cooling in similar processes. No flow and pressure are required for cooling. The oil path of the original system is completely returned to the tank through the PQ valve, doing no useful work, wasting energy.
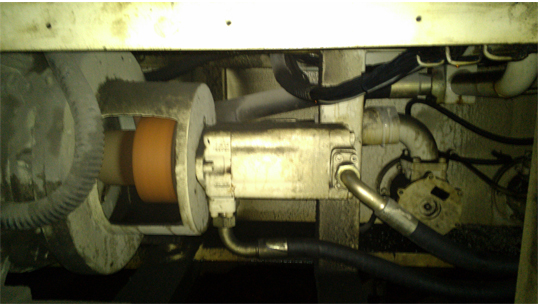
Figure 2: The original machine control
3, HID618A series servo drive energy saving control
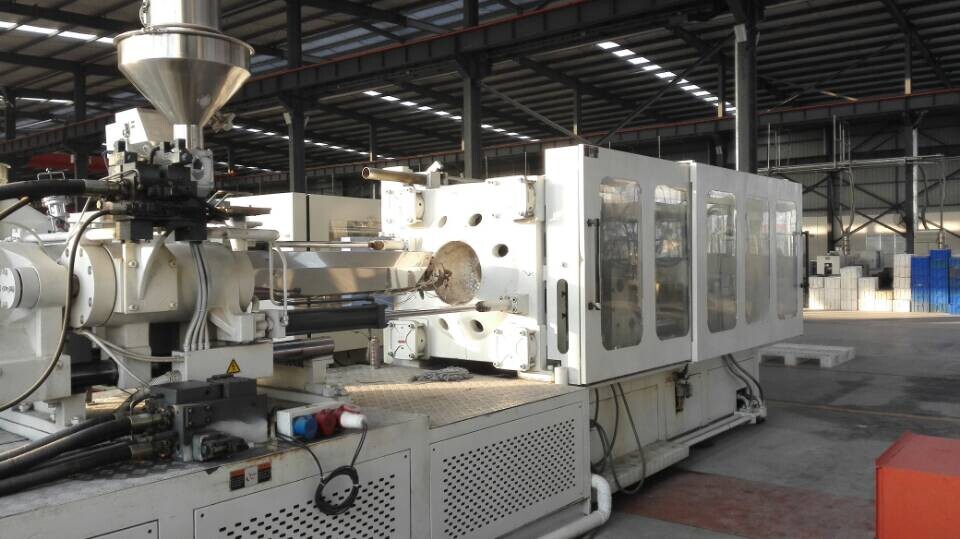
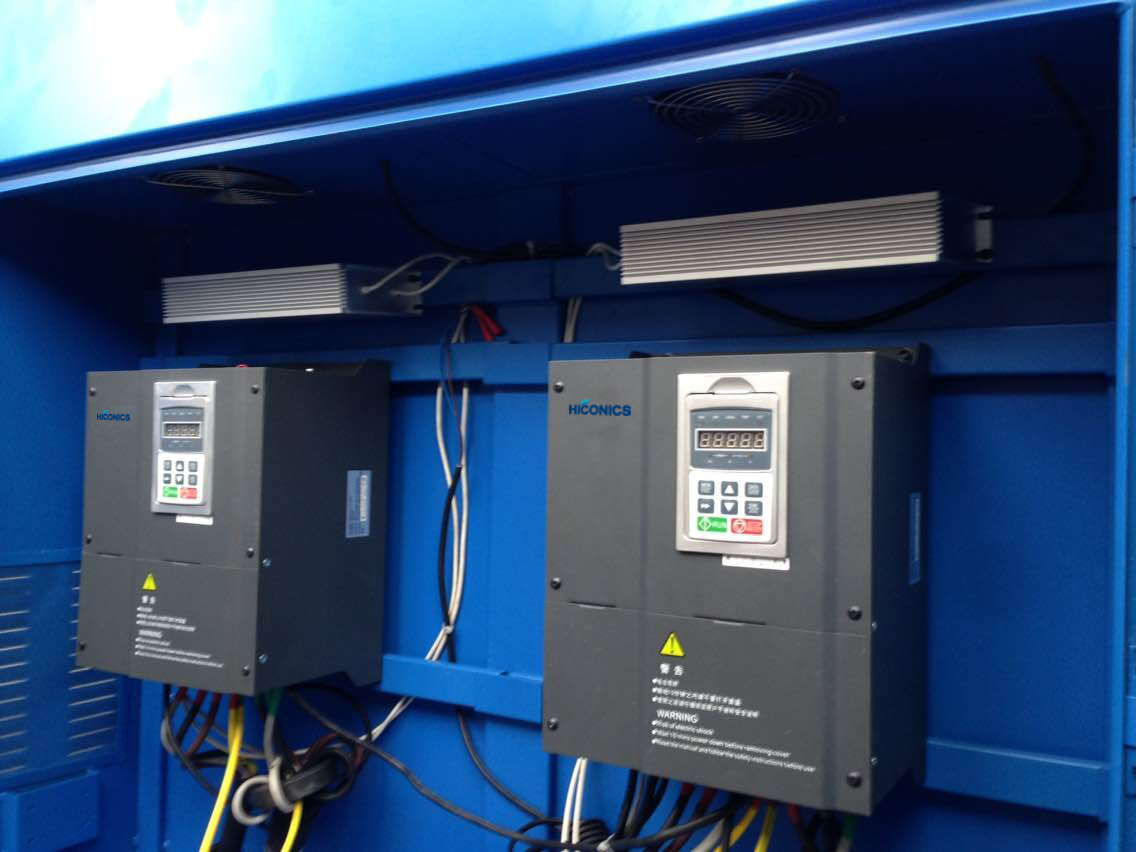
4ã€HID618A series servo driver installation method A, main circuit connection:
The power cable is connected to the main circuit RST of the driver, the motor cable is connected to the main circuit UVW, and the brake resistor line is connected to the driver's main circuit "+" and "PB". The ground wire is connected to the main circuit PE of the driver. The motor fan wire is connected to the main circuit terminal RST or other three-phase power supply.
B, control board signal line connection:
Positive pressure signal line is connected to the control board AI1, the negative electrode is connected to the control board GND;
The positive of the flow signal line is connected to the control board AI2, and the negative pole is connected to the control board GND;
The positive pressure sensor is connected to the control board 15V, the negative electrode is connected to the control board AI3-, and the signal line is connected to the control board AI3+;
The motor temperature output line is connected to the control board DI6 and COM;
Injection molding machine motor enable signal line received control board DI1 and COM;
The encoder cable is connected to the control board DB9 port.
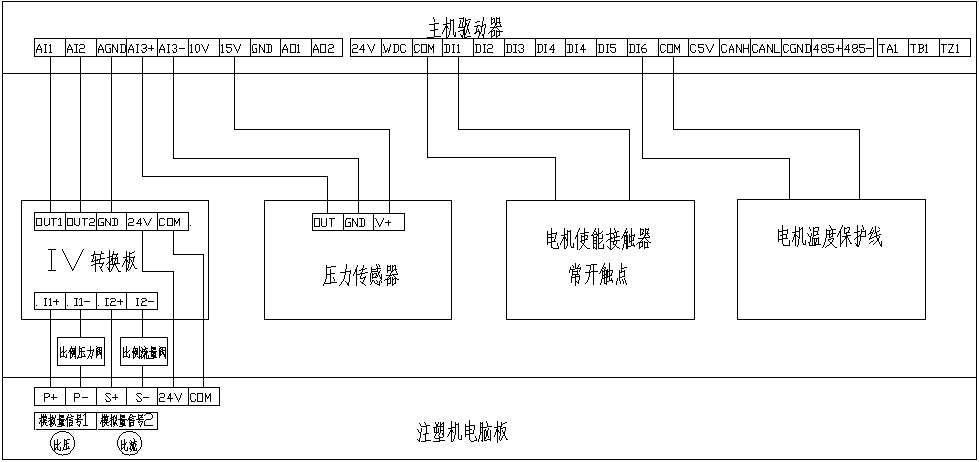
Figure 3: HID618A driver control circuit wiring diagram
Second, the HID618A series of drivers in the Gu technology application of the effect of a high energy-saving rate. Gudi's injection molding products are mainly PPR and UPVC pipe fittings. The HID618A dedicated drive controls the output of the motor in real time according to demand. The motor speed is almost zero when the pressure is maintained and the cooling is achieved. This saves a lot of energy for the customer. .
2, reduce the oil temperature. The HID618A dedicated drive cooperates with the servo energy-saving system to replace the system relief valve and proportional valve. According to different process requirements, different flow rates are provided on demand, which effectively suppresses the overflow of the oil circuit, reduces oil circuit circulation, and reduces oil temperature.
3, reduce noise. After applying the HID618A dedicated driver, the overall operating noise is significantly lower than that of the original asynchronous motor vane pump control system, improving the ambient noise.
4, to improve the control accuracy. HID618A dedicated driver, the application of advanced software algorithms, high control accuracy, pressure fluctuations in ± 0.5bar, product repeatability is good.
5, easy to use. HID618A servo dedicated driver, user-friendly design, easy to install and use, using common motor parameters packaged form, to avoid cumbersome motor parameter input. The pressure and flow curve calibration adopts 11 percentage sampling points. The optimization of curve calibration also brings user-friendly use.
Third, the small combination of Kang HID618A series of special injection molding machine servo drive with its outstanding performance in Chongqing Gu Di Technology and Ezhou Gudi technology batch applications of 55 units, the average power saving rate reached more than 35%, high product repeatability, stable production . After several months of operation, it has been operating stably with a 100% operating rate and zero failures. It has been highly recognized by customers and worthy of widespread promotion.
stainless steel pig trough for piglets feeding equipments
1.pigs can clearly see the food, a eat enough.
2. pig drinking water was significantly more than 30% savings in water, reducing sewage and sewage treatment pressure.
3. to prevent the metal drinking water to scratch the pigs, to avoid the chance of traumatic infection.
Feeding Trough,Piglet Feeding Trough,Piglet Feeder Feeding Equipment,Trough Piglet Feeder For Pig
Ningbo New Glory International Trading Co.,Ltd , http://www.stock-farming.com